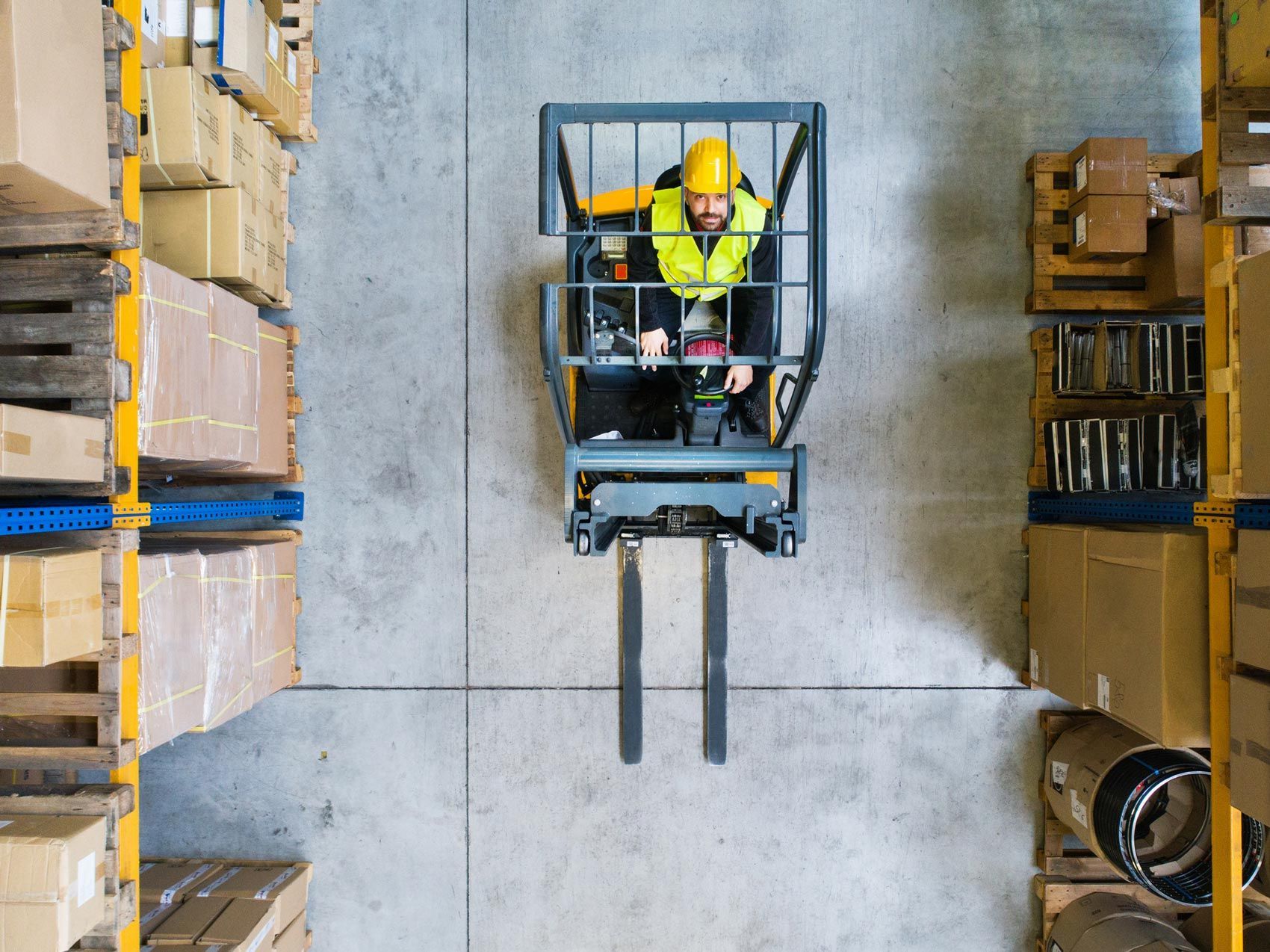
If your warehouse relies on pallets, you face additional safety risks that could be a liability to your business. One key to minimizing this added danger is to understand and implement good safety practices regarding those pallets. To help you move toward a safer and more profitable warehouse, learn about three categories of pallet safety to focus on.
1. Fire Danger
Any business that stores and utilizes a lot of pallets faces the threat of fire. Stacks of pallets can often be some of the most combustible items within your warehouse. Even individual pallets stacked with certain materials could add to the fire hazard.
Reduce fire danger by thinking proactively about your warehouse layout. If possible, create a separate location outside the main warehouse area in which to store excess pallets. Inside the building, ensure that your fire suppression system meets National Fire Protection Association guidelines for any space that stores pallets. And, put space between stored pallets so that you have less combustible material in any one area.
Finally, utilize fire-retardant materials around the pallets - things such as packing materials for the goods, organic materials on the pallet racks, and items on the walls or floor around them.
2. Falling Danger
Pallets and their loads are in danger of falling due to various issues. A stack of pallets can become unstable, particularly once it exceeds about six feet high or is stacked incorrectly. The pallet itself could be damaged, rotten, or aging, resulting in breakage and falling. The shelving system could also be inadequate or damaged. And those who move or transport the pallets could do so haphazardly.
A reduced danger of potential spills and falling pallets begins with good inspection habits. Every time a team member handles a pallet, inspect it thoroughly quality issues like breakage, cracking, rot, loose or exposed nails, and bending or bowing. Have replacement pallets handy in case your staff finds anything that concerns them.
Combine pallet inspections with regular pallet rack inspections. Check the uprights, footplates, beams, bracing, decking, and beam locks on a set, posted schedule. In addition, users should regularly inspect the racks as they do their work. Once again, if they have concerns, remove that rack from service until you can address the problem.
Another important step in preventing dangers is regular training of your workers and incentives to put into practice what they learn. If you, as management, make safety a priority, your employees are more likely to follow suit. Take proactive steps, such as implementing a more efficient pallet rack system, so that employees aren't forced to stack pallets too high or on their sides.
3. Tripping and Piercing Danger
Anyone who works around pallets must move and work defensively so as to avoid tripping, stepping on nails and other hazards, or handling dangerous materials. But busy warehouse employees often fail to - or cannot afford to - take the time and energy to do things in the safest manner. Management must act proactively if it wants to reduce this risk.
Start a better system by talking with employees about their concerns or common mishaps. Do they have personal protective equipment? Make this a priority in your company. Are they too busy to take safety steps? Consider ways to provide relief to the warehouse. Do they have to walk over pallets, under racks, between forklifts, or through debris? Clear the floor, minimize clutter in work areas, and widen traffic paths.
Safety should be a key goal for all companies, and improvements in the warehouse are a great place to make a big impact. Want to know more about how to boost safety within your own business? Start by talking with the warehouse experts at Lone Star Pallet Rack today.