4 Ways to Maximize the Efficiency of Your Warehouse
- By Admin
- •
- 03 Jan, 2020
- •
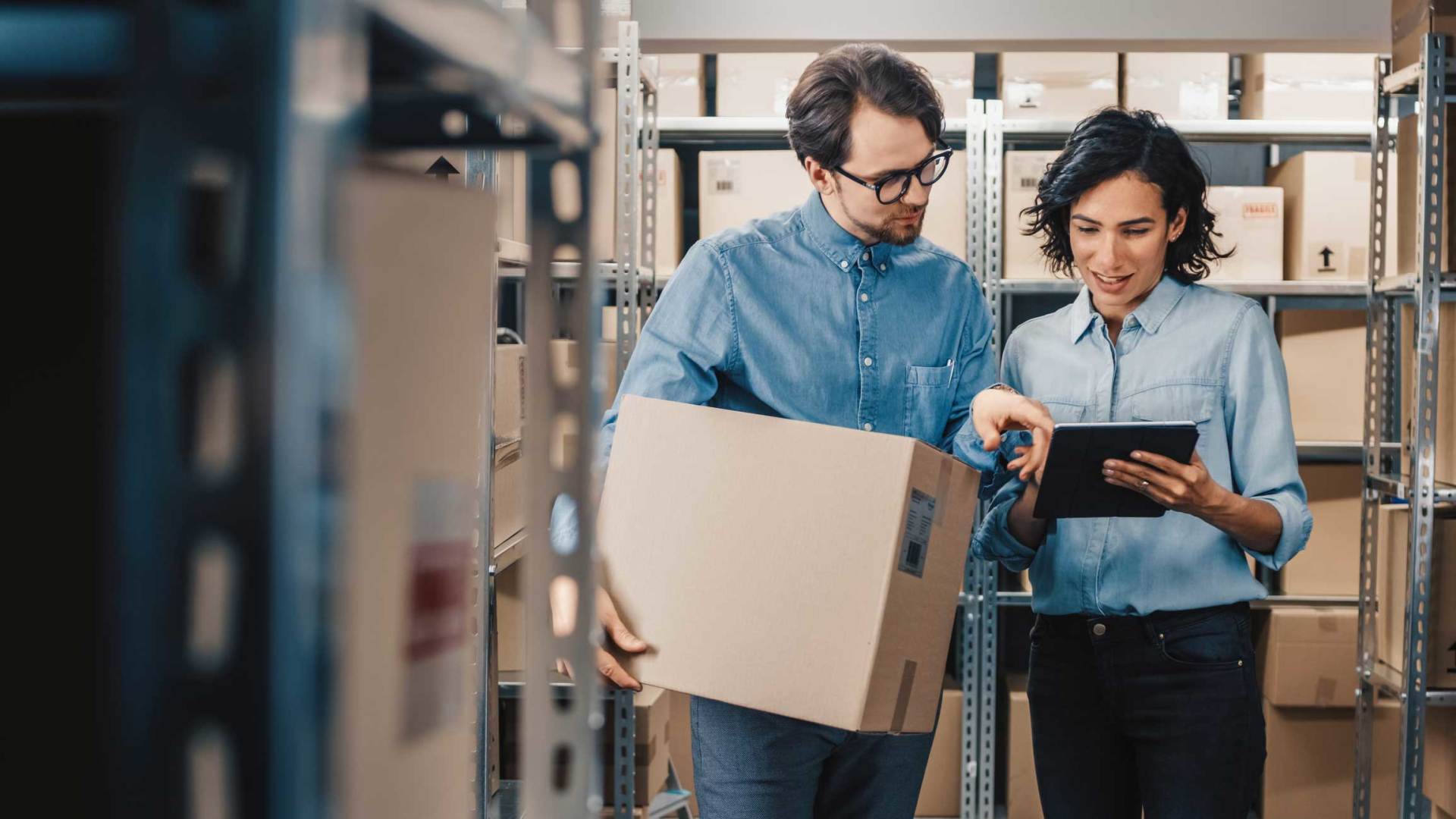
How well does your warehouse operate? For most companies, this critical and well-used segment of the business can always use physical improvement as well as lowered costs. One key way to accomplish both is to maximize the physical efficiency of the space. How can you do this in your own warehouse? Here are four steps to take.
1. Sketch It Out
Before you attempt to move any racks or stations in the actual building, plan out everything on paper. In fact, this should take a much larger percentage of your planning time than actually setting up the warehouse.
During this phase, turn the space requirements previously identified into actual blocks on the layout. Add in auxiliary services such as forklift paths, pedestrian walkways, storage, and offices. Then move around the various components to look for new and potentially better ways to place them.
Even after you physically set up the warehouse, go back to this step occasionally to continue to find better alternatives and troubleshoot inefficiencies that come up.
2. Identify Space Needs
Having the right amount of space for each inventory item and segment is key to using the warehouse as efficiently as possible. The goal is to provide enough space for goods to be organized and easily accessible without leaving large unused space.
Start at the most basic level and determine how much physical space each of your inventory items need. A carpet facility might count this in terms of individual rolls of carpeting. An auto parts business might use the size of standard bins of each part (rather than the part itself). Then multiply the amount of space you have by your average (or high season) number of units.
Turn these calculations into an overall space requirement for each segment - usually each product line, product type, or department. Along with these measurements, make note of any special requirements, such as refrigeration or ventilation.
3. Follow the Flow
How do inventory goods flow through the space? Test your system by imagining the path each different inventory item takes. Follow the path of more popular goods as well as those that sell less often.
As you move through the virtual warehouse, think about the routes. Are popular goods stored close to shipping for easy access? Are they blocked by less popular goods? How do pickers reach each item? How far does the item travel into, around, and out of the warehouse? Does the item take the most direct routes?
4. Look for Waste
As you analyze the flow of people and assets, look for indications of waste - which, in efficiency terms, includes any unnecessary or redundant step taken by a person, a document, an inventory item, or a procedure. Waste includes not only physical movement but also intangible steps, such as requiring unnecessary signatures on a document. Waste in any form represents lost time, money, and assets.
How might you fix waste in the warehouse? Do pickers take circuitous paths through the warehouse? You might consolidate groupings. Do you have unused space above pallet racks? Reorganize storage to use vertical space better. Are pickers pulling wrong items? Investigate further to reduce redundant movement. Does packing material take up space? Consider a customized packing solution instead.
Whether you want to set up a new warehouse or overhaul your existing facility, follow these steps to make the process as efficient as possible. And if you need more ideas or help, start with a call to the warehouse experts at Lone Star Pallet Rack. From rack design and implementation to additional warehouse services, our inventory includes everything you need to design a modern, efficient, and useful space.
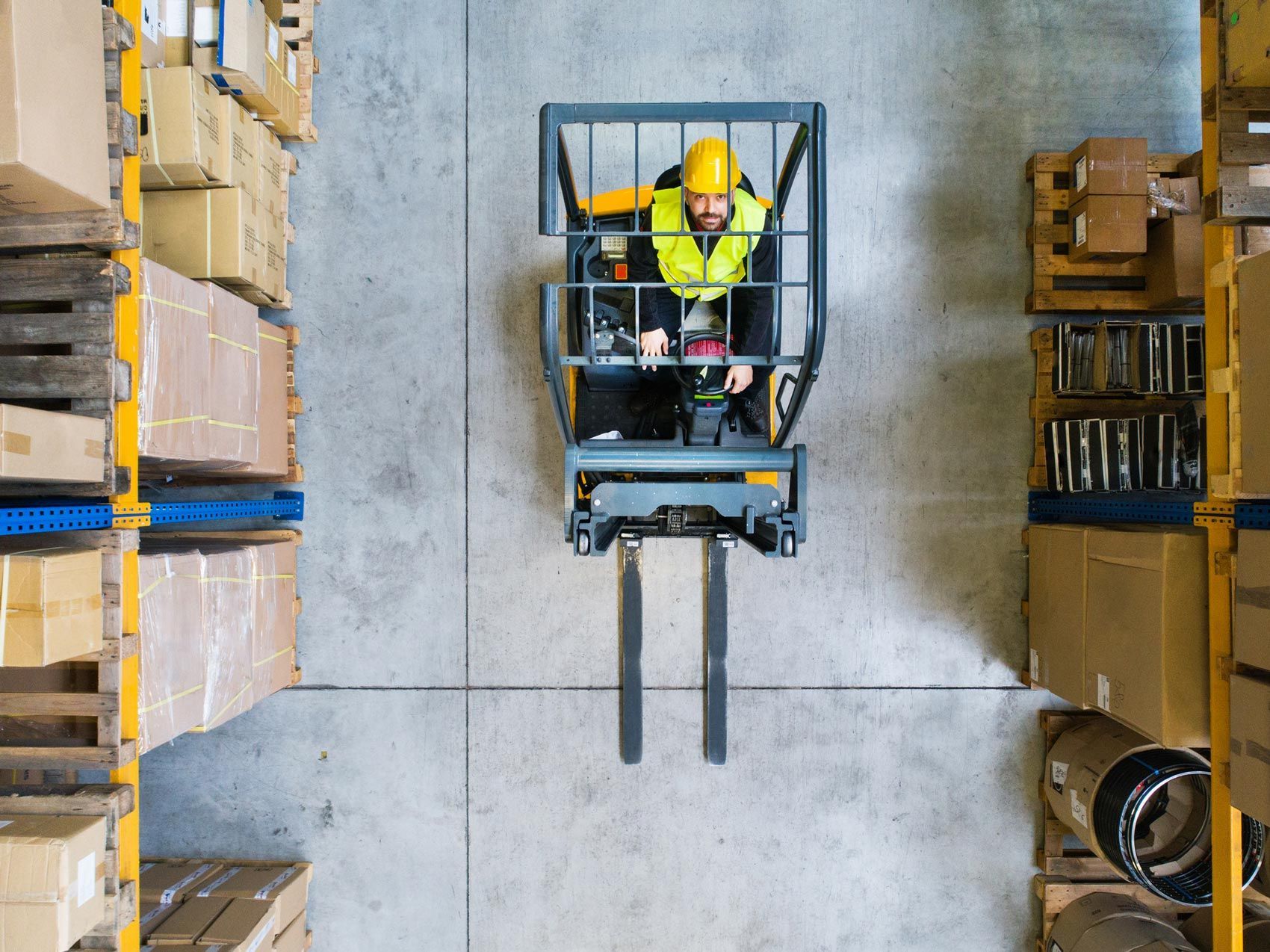