5 Warehouse Pallet Racking Mistakes You Should Avoid
- By Admin
- •
- 01 Jul, 2021
- •
Pallet racking systems are the foundation of warehouses or any storage facility. They help to drive productivity, efficiency, and speedy operations in the workspace. However, pallet rack mistakes can raise safety concerns for your personnel and your equipment, not to mention creating inefficiencies as well.
Mistakes are costly, dangerous, and not worthwhile for your business. Here are warehouse pallet racking mistakes you should avoid.
1. Incompatible Rack Systems
There are multiple types of racking systems you can implement in your warehouse, including drive-in, drive-through, selective, and push-back models. Each of these systems has its order of operations that support or are incompatible with your warehouse regarding speed, accessibility, productivity, and efficiency.
Therefore, you must consider the materials you store, the size or space of your warehouse, the type of equipment and vehicles you will use, and the order of operations in your plant to guide you to which racking system is best for your warehouse.
You must also consider the height to depth ratio. The Rack Manufacturers Institute (RMI) recommends that you evaluate the height to depth ratio (HTD) ratio to determine the stability of a single row of standard steel storage racks.
The stability ratio may vary from 1:1, 6:1, or 8:1 for each system, but there may also be safety concerns. Engineers must address an unstable racking system to mitigate risks of collapse, leading to property damage or injury to staff.
2. Overloaded Racks
Different pallet rack systems can withstand different loads. Still, ISO pallet standard sizes carry approximately 2,000 pounds of static load, and the racks will have a centerline beam that can support 2,000 pounds on either side of the aisle.
Maintaining maximum load at all times ensures that you don't cause irreparable damage to the frame of the racking system, which can give way to the excess weight collapsing and damaging your inventory. Moreover, overloaded pallet racks can also damage your plant, forklifts or other equipment and injure your operators.
Ensure you stay within the limit for capacity, and can also post maximum load capacity signage against every rack to ensure compliance.
3. Faulty Rack Systems
You can get second-hand reputable racking systems but be very wary about them. If you want to install second-hand racks, make sure to have a professional inspect their quality; otherwise, you'll have to pay additional costs for repair in faulty systems.
Therefore, no matter how pressed for cash you are, never negotiate on quality or choose cheap systems with underlying issues like internal corrosion. These problems will need repair in the future, costing you significantly more than the initial cost.
4. Missed Rack Protection
Rack safety is essential to your business, your property, and your staff. When putting up a racking system, ensure that pallet protection is added to ensure your investment's safety. Examples of racking protection you can install include inside wrap barriers, angle and corner post protection, load signage, frame end guards, guard rails, and floor channels for drive-in racking.
5. Irregular Maintenance and Repairs
Maintenance and repair are very vital because your pallet racks are bound to suffer some wear and tear. Take advantage of regular inspections and annual safety audits to check wear and tear on your racking systems, overloaded beams, and damaged equipment.
Additionally, you must be proactive in repairs to avoid irreparable damage to your equipment and to maintain productivity and efficiency in the workspace.
Bottom Line
For every pallet racking system, consider your investment and the need to expand because this will keep you focused on optimizing the use of your pallet racking system. Avoid these five mistakes if you want to secure your investment.
If you'd like more information about pallet racking systems, don't hesitate to contact us.
Mistakes are costly, dangerous, and not worthwhile for your business. Here are warehouse pallet racking mistakes you should avoid.
1. Incompatible Rack Systems
There are multiple types of racking systems you can implement in your warehouse, including drive-in, drive-through, selective, and push-back models. Each of these systems has its order of operations that support or are incompatible with your warehouse regarding speed, accessibility, productivity, and efficiency.
Therefore, you must consider the materials you store, the size or space of your warehouse, the type of equipment and vehicles you will use, and the order of operations in your plant to guide you to which racking system is best for your warehouse.
You must also consider the height to depth ratio. The Rack Manufacturers Institute (RMI) recommends that you evaluate the height to depth ratio (HTD) ratio to determine the stability of a single row of standard steel storage racks.
The stability ratio may vary from 1:1, 6:1, or 8:1 for each system, but there may also be safety concerns. Engineers must address an unstable racking system to mitigate risks of collapse, leading to property damage or injury to staff.
2. Overloaded Racks
Different pallet rack systems can withstand different loads. Still, ISO pallet standard sizes carry approximately 2,000 pounds of static load, and the racks will have a centerline beam that can support 2,000 pounds on either side of the aisle.
Maintaining maximum load at all times ensures that you don't cause irreparable damage to the frame of the racking system, which can give way to the excess weight collapsing and damaging your inventory. Moreover, overloaded pallet racks can also damage your plant, forklifts or other equipment and injure your operators.
Ensure you stay within the limit for capacity, and can also post maximum load capacity signage against every rack to ensure compliance.
3. Faulty Rack Systems
You can get second-hand reputable racking systems but be very wary about them. If you want to install second-hand racks, make sure to have a professional inspect their quality; otherwise, you'll have to pay additional costs for repair in faulty systems.
Therefore, no matter how pressed for cash you are, never negotiate on quality or choose cheap systems with underlying issues like internal corrosion. These problems will need repair in the future, costing you significantly more than the initial cost.
4. Missed Rack Protection
Rack safety is essential to your business, your property, and your staff. When putting up a racking system, ensure that pallet protection is added to ensure your investment's safety. Examples of racking protection you can install include inside wrap barriers, angle and corner post protection, load signage, frame end guards, guard rails, and floor channels for drive-in racking.
5. Irregular Maintenance and Repairs
Maintenance and repair are very vital because your pallet racks are bound to suffer some wear and tear. Take advantage of regular inspections and annual safety audits to check wear and tear on your racking systems, overloaded beams, and damaged equipment.
Additionally, you must be proactive in repairs to avoid irreparable damage to your equipment and to maintain productivity and efficiency in the workspace.
Bottom Line
For every pallet racking system, consider your investment and the need to expand because this will keep you focused on optimizing the use of your pallet racking system. Avoid these five mistakes if you want to secure your investment.
If you'd like more information about pallet racking systems, don't hesitate to contact us.
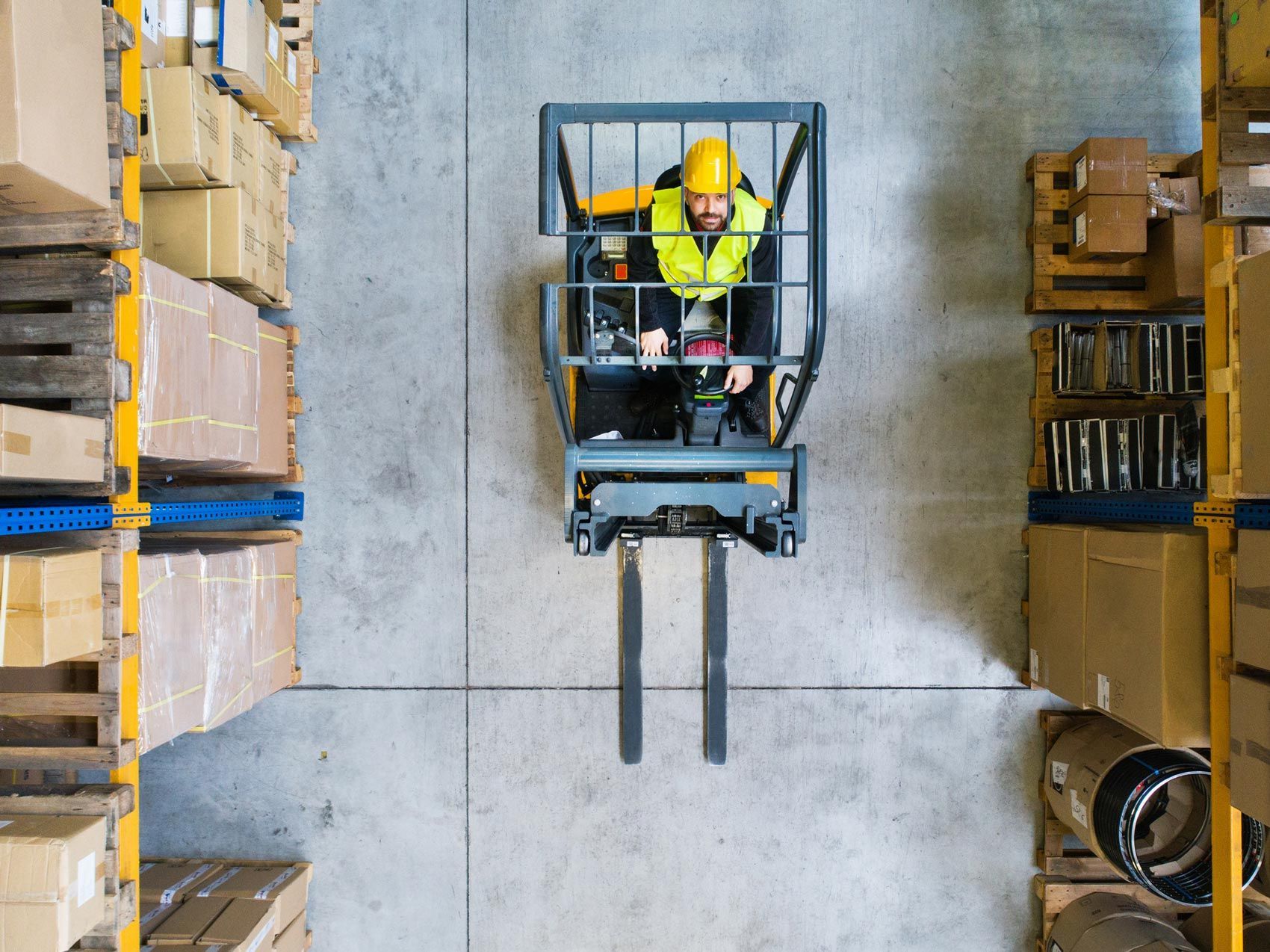
Learn essential warehouse safety practices to protect your workforce and enhance operational efficiency. Discover tips on proper storage, equipment maintenance, PPE, and emergency preparedness to create a safer work environment. Explore best practices for reducing risks and keeping employees safe while maximizing productivity in your warehouse.
Read this article to learn how pallet racks can optimize office space, improve organization, and enhance productivity in your workplace efficiently.
Clear film is an essential resource in any warehouse. Read our blog to learn what key considerations to keep in mind when selecting clear packing film.
A pallet jack is essential equipment for any warehouse. Read our blog to learn what to consider when getting a pallet jack for your warehouse.
If you need to maximize the space in your warehouse or storeroom, consider a push-back pallet rack system. Take a look at how push-back systems work.
If you need to maximize the space in your warehouse or storeroom, consider a push-back pallet rack system. Take a look at how push-back systems work.