Drive-In Pallet Rack Benefits Your Warehouse Needs Now
- By Admin
- •
- 10 Mar, 2021
- •

Warehouse space is in greater demand as more online shoppers click to make their purchases. In fact, experts estimate by 2025 an additional one billion square feet of space may be necessary. Your warehouse might need to make some adjustments to stay competitive.
Drive-in pallet rack systems are a storage method where a forklift directly enters a long drive-in bay to stash pallets rather than from an aisle. This unique method provides several advantageous storage options. Consider these drive-in rack system benefits your warehouse needs now.
Drive-in Systems Eliminate Warehouse Aisles
Unlike traditional aisle pallet racks, drive-in pallet rack systems consist of several rows of deep pallet bays. There, pallets go on support rails that attach to upright posts. To stash a loaded pallet, a forklift first enters the bay and approaches the first available support rail at the end. The lift then places the load once it is elevated to the appropriate height of a support rail.
The drive-in concept means you can eliminate some warehouse aisles or at least keep aisles to a minimum. Drive-in systems do not require access aisles in order to drop or retrieve loads. Fewer warehouse aisles reduce wasted space and increase the warehouse square footage you can devote to valuable storage space.
Drive-in Systems Accept Any Forklift Equipment
Warehouses with several styles of forklifts discover compatibility issues if access aisles or other spaces are too narrow for accommodate forklifts with a larger turning radius. Fortunately, you can continue to use your existing forklift equipment when you utilize customizable systems like the drive-in pallet configuration.
Many types of drive-in pallet systems are customizable. You can specify the desired width and height of support rails you require for your storage needs. This feature allows you to align your system dimensions to your forklift equipment. When your drive-in system accepts any type of forklift equipment, you do not need to invest in new or different forklift equipment.
Drive-In Systems Let You Diversify Your Products
Drive-in systems follow the last-in, first-out inventory model, or LIFO. This means products placed first must come out last as newer products are more accessible and available. Because drive-in systems are incredibly dense, products are usually accessed less frequently.
With the help of drive-in pallet systems, you can diversify the types of products your warehouse has to include items with very long life spans or that are not time sensitive. Also, you can include like items in huge quantities you will probably only move one or two times. For example, large shipments of holiday-specific party goods in October or November are sure to be gone in December.
Finally, drive-in pallet systems can be useful in temperature-controlled spaces like a cooler or freezer. The compact nature of stored products in a drive-in system means you can optimize a chilly yet expensive storage space.
Drive-In Systems Can Adapt to Drive-Through
Your warehouse may discover a need for high-density storage but with access at two ends rather than one. Rather than drive in to leave or retrieve inventory goods, you can adopt a drive-through system with better inventory flow.
Drive-through systems let you stash and retrieve goods from either end, with each end usually devoted to one task. This system lets you change your inventory model from LIFO to FIFO, or first-in, first-out. Inventory placed first will come out first.
Drive-through systems still offer incredible amounts of storage space like the drive-in system. If you are not sure which is best for your warehouse, contact Lone Star Pallet Rack. We can help you measure your space and choose the right pallet system for your configuration.
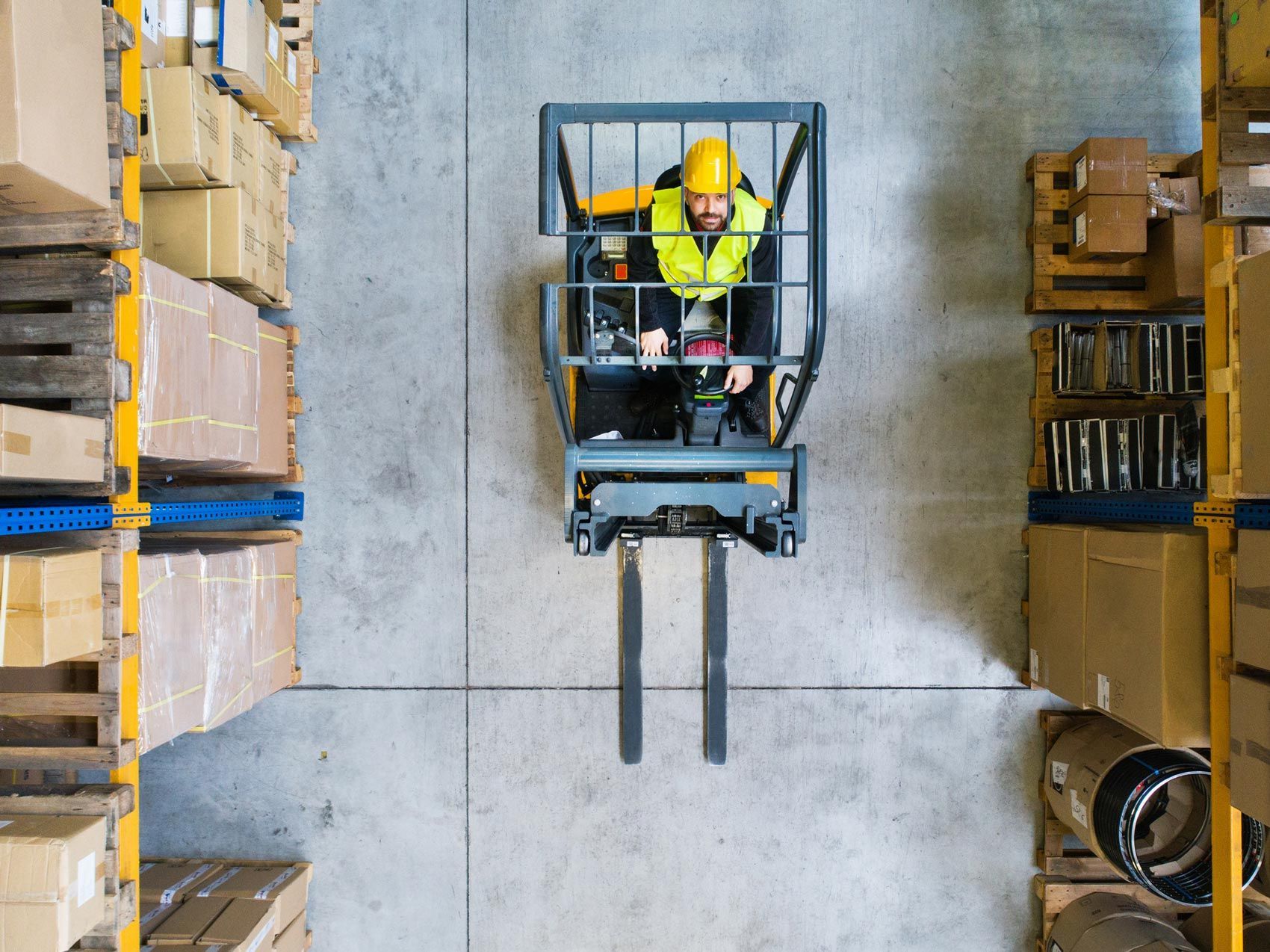