FIFO and LIFO - Do You Need More Organized Inventory Picking?
- By Admin
- •
- 06 Jan, 2021
- •
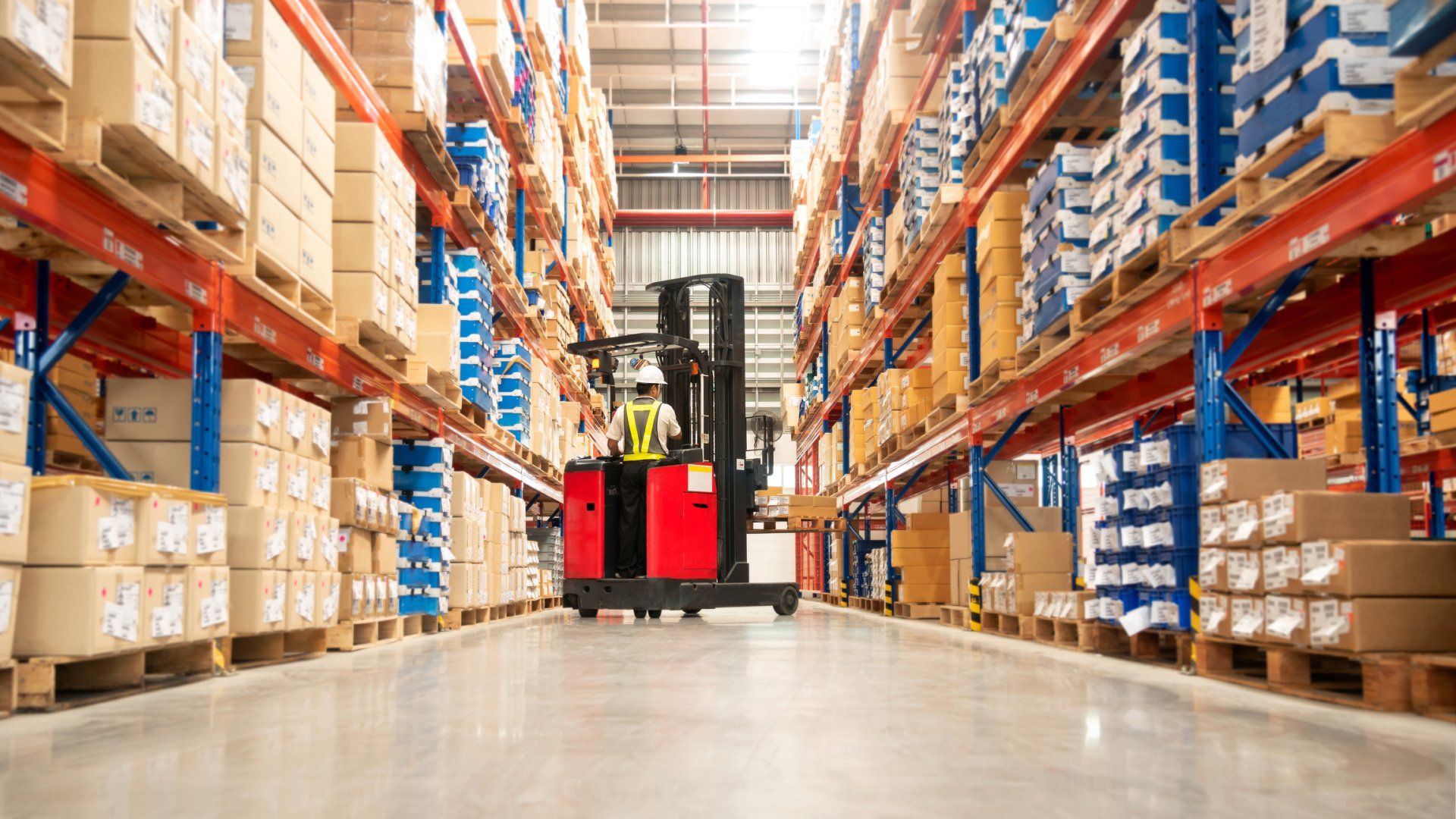
How do you select and pull items from the inventory in your warehouse? Many small businesses begin with a somewhat haphazard method of pulling inventory, often taking the first item found regardless of how long or short it may have been in inventory.
But should you switch to a more structured method for picking goods? For most businesses, the choice is largely down to LIFO versus FIFO. What do these mean and how would you implement them? Use this short guide to inventory-pulling methods, and learn how they can affect your warehouse operations.
What Is FIFO and How Does It Benefit?
FIFO stands for first in, first out. With this inventory selection method, you would take out the oldest inventory item in its category and use it first. FIFO is generally used by any company with perishable goods or those that may get damaged over time. This might range from foodstuffs or plants to things like batteries or goods that oxidize or are stored outside. FIFO ensures that nothing expires or becomes too old to use.
What Is LIFO and How Does It Benefit?
LIFO, in contrast, refers to last in, first out. The perks of choosing this method are often less obvious. By taking the newest items off the shelf when you need inventory, you better match up current inventory costs with current sales. You may also be able to keep updated in a rapidly-changing market.
The accounting benefits of LIFO tend to be the driving force behind this picking method, but it may also increase efficiency if your products won't expire or age quickly. After all, if you can simply place inventory anywhere and use it - without worrying about fitting it into specialized locations behind other goods - your warehouse staff saves time, space, and effort.
Why Does Picking Method Matter?
As your inventory grows, the risks of mismanagement grow as well. If you don't carefully ensure that older items are used in time, you waste money on unsold items. You also may not find out about defects or other damage until long after you can do anything about it. And you can only maximize the efficiency and usage of your warehouse storage system if everyone uses the same picking methods.
How Can You Implement Your Method?
Whether you decide that LIFO or FIFO inventory is right for some or all of your warehouse, choose the warehouse systems that best fit it.
For example, if you choose FIFO, you might install a gravity-fed pallet flow rack system. With this system, personnel load new inventory to the back of sloped racks. As a pallet is removed from the front, the racks automatically push the next oldest pallet to the front. This increases efficiency but can only work with a FIFO system. And a drive-in storage system allows personnel to enter the rack itself and pull from anywhere.
A company that utilizes last in, first out picking, on the other hand, might use drive-through pallet racks instead. The forklift enters the racks and pulls its goods, then it leaves by the opposite exit route. By keeping the machinery flowing in one direction, you can place new pallets in the racks without risking any hazardous or inefficient conflict with pickers pulling out pallets at the same time.
Where Can You Learn More?
Do you need to better manage how your inventory is pulled? If so, start by learning about the many pallet rack options available to today's businesses. At Lone Star Pallet Rack, we can help you find the right storage methods for LIFO, FIFO, or even a hybrid system that fits your needs. Call today to make an appointment or speak to a warehouse pro.
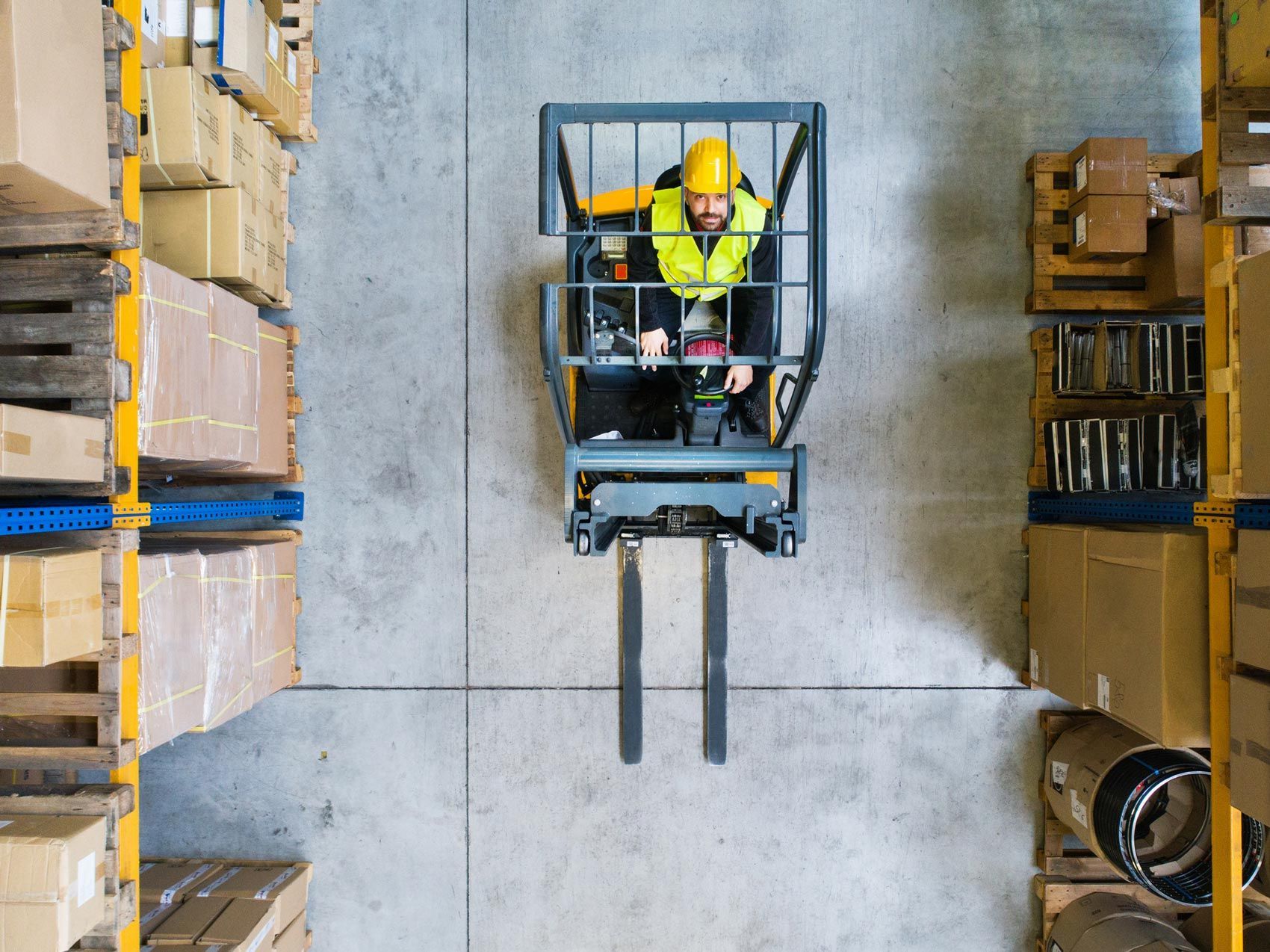